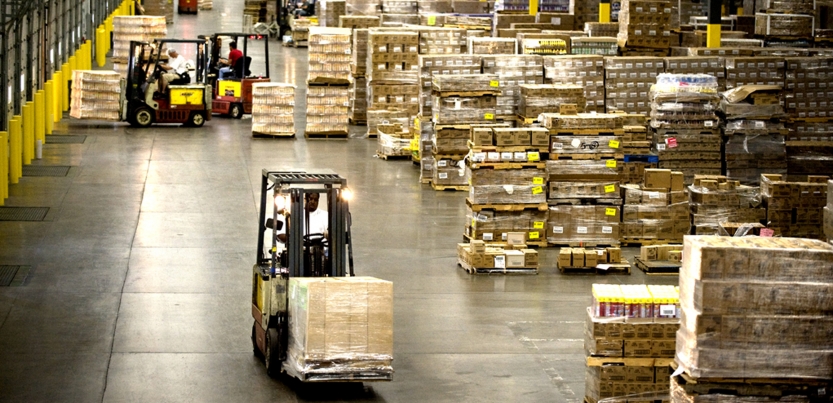
In the 1970s and 1980s, big manufacturers moved plants out of cities like Detroit and outsourced aspects of production to plants “out on the interstate” to get away from those concentrations of blue-collar workers and unions. Now they have had to concentrate thousands of workers in crossroads of transportation and warehouse clusters. These are the Detroits of today. Credit: Davis Turner, CC 3.0
A factory fire recently illustrated just how vulnerable are the supply chains at the heart of the global economy. The fire was at a single supplier—yet it forced Ford to temporarily halt production of the nation’s bestselling truck, the F-150.
Think how much leverage workers could have if we acted like the fire.
This is exactly how large-scale organizing happened in the auto industry. In late 1936, members of the newly organized Auto Workers (UAW) struck several General Motors plants to win union recognition. A month later, GM still hadn’t budged.
But in February 1937, workers in Flint, Michigan, occupied Chevrolet Plant 4. In less than two weeks, one of the most powerful corporations on earth capitulated.
What made the Flint plant occupation so much more powerful than the prior strikes? It was Chevy 4’s strategic position: this single plant made all the engines for Chevrolet, and its occupation shut down GM plants throughout the country. The Flint victory set off a wave of sit-down strikes and union wins across the country.
The introduction of just-in-time parts delivery has made today’s supply chains even more vulnerable. Consider the 1998 strike at two UAW locals in Flint. It shut down 25 assembly plants, which soon lacked key parts, and hundreds of suppliers from Canada to Mexico, which had no place to send their parts and no room to store them.
In fact, a careful study of the way products travel in the 21st century reveals promising opportunities for large-scale organizing.
LARGE VOLUME, FAST PACE
The pace and volume of goods moving around the U.S. has increased dramatically over the past 20 years:
- Measured in dollars, the amount of freight doubled from 1998 to 2017.
- Over those years the number of warehouses and distribution centers grew by two and a half times, to 17,000.
- The size of warehouses and distribution centers increased dramatically as they became the sites of product movement rather than storage. Their workforce more than doubled from 1990 to 2017, to 840,000.
- Intermodal ground transport by truck and rail increased fivefold in a decade, from 43 billion tons in 2002 to 214 billion in 2012.
- Beginning in the 1990s and accelerating with the rise of e- commerce, older forms of information technology such as bar codes and GPS were joined by newer ones such as electronic data interchange (EDI) and radio frequency identification (RFID). These technologies track and guide the movement of goods and workers more rapidly and reliably, allowing for the dramatic expansion of just-in-time inventory systems.
All this requires vast sunk capital investments. The roads, rails, ports, airports, and railroad switching and intermodal yards that make up supply chains can’t be picked up and moved far, since they are located to deliver goods to specific urban markets. Nor are many of the 10,000 giant warehouses built since the late 1990s about to pull up anchor.
Where these transportation networks converge, you’ll find huge “clusters” that include warehouses, information technology centers that track and guide goods, and intermodal yards where containerized goods move from trucks to trains and vice versa.
In the U.S., there are 61 such giant clusters, which receive and send goods for major manufacturers as well as for large retailers like Walmart and Amazon. With high fixed costs, they’re vulnerable to expensive disruptions, including worker actions.
Enhancing this vulnerability is manufacturers’ and retailers’ obsession with what logistics gurus call “time-based competition.” This means not only just-in-time delivery aimed at minimizing inventory costs, but also a race to get goods to customers faster than the competition. It’s how Walmart beat K-Mart, and how Amazon is beating Walmart. It’s also one way Toyota beat GM.

The same gurus admit that the fast pace makes the system vulnerable when things go wrong, as they often do. A hurricane, a slowdown in a port, or a strike at a supplier can create a costly “ripple” along the whole supply chain.
DETROITS OF TODAY
Supply chains aren’t just the physical infrastructure of factories, roads, rails, warehouses, ports, and the equipment that moves things around. They’re also clusters of labor.
For all the technology, without the hand and mind of labor, things stop. Even Amazon’s famous Kiva robot, which electronically identifies and mechanically picks products from giant racks, becomes so much dead capital when the worker to whom it delivers a product isn’t there.
Even setting aside the millions of manufacturing and retail workers who are also part of supply chains, the number of U.S. workers directly involved in logistics, such as warehouse workers, truck drivers, and port workers, has been estimated at 3.2 million, mostly blue-collar. And this doesn’t include the 160,000 or so railroad freight workers, the half-million postal workers, the fluctuating numbers of construction and utility workers, or the unknown numbers of IT workers.
Furthermore, 85 percent of these logistics workers are concentrated in major metropolitan areas:
- Metro Chicago employs 160,000 workers in logistics jobs.
- FedEx’s Memphis “aerotropolis” has 220,000.
- Southern California’s “Inland Empire” warehouses have 100,000, not including port workers.
- Logistics Park north of Fort Worth, Texas, employs 93,000 workers directly or indirectly.
- Louisville’s UPS hub has 55,000.
In the 1970s and 1980s, big manufacturers moved plants out of cities like Detroit and outsourced aspects of production to plants “out on the interstate” to get away from those concentrations of blue-collar workers and unions. Now they have had to concentrate thousands of workers in crossroads of transportation and warehouse clusters. These are the Detroits of today.
ORGANIZE?
There are, to be sure, many barriers to organizing. Most port truckers are still classified as “independent contractors,” while about 60 percent of warehouse workers in major clusters such as Chicago and Los Angeles are employed by temporary agencies.
On the other hand, many of the long-distance and local truckers who make up about 40 percent of the logistics workforce are union members. So are the UPS, railroad, and postal workers who move things in and out of these clusters and along supply chains. These union workers could flex their power of disruption to help nonunion workers organize.
Within some of the biggest clusters there are ongoing organizing efforts. In the Chicago area, for example, the worker center Warehouse Workers for Justice has won big claims for back pay, put an end to brutal forms of piecework where crews were paid by the truckload, and pulled off a series of strikes in Walmart’s giant warehouse in 2013.
Similar organizations exist in the Los Angeles and New Jersey clusters. With 15 strikes in four years, some port truckers in L.A. organized by the Teamsters have won employee status and even union recognition. But it’s clearly going to take a lot more to win on a large scale.
One of the biggest sources of potential power is to be found among the hundreds of thousands of rank-and-file union members who may not work in logistics themselves, but work in the same big metro areas as these clusters. Mobilize even a tiny percent of these workers to support unorganized warehouse, transportation, and IT workers, and there could be an upsurge that sets off a new wave of organizing.
Kim Moody is a founder of Labor Notes and author of On New Terrain: How Capital Is Reshaping the Battleground of Class War (Haymarket Books, 2017). He lives in London and is a member of the National Union of Journalists.